Twin Screw Sheeter is a perfect replacement for dump-mill and sheeting mill combination in a traditional rubber mixing line. TSS takes mix compound directly discharged from an internal mixer into its hopper chute and converts it into a continuous, seamless rubber sheet that is then fed into a Batch-Off Cooling Line. Bainite offers customized TSS with latest technology. Apart from the power, space and labour saving, the material self-fed in TSS gives high quality of mix consistently. TSS keeps the environment clean and is safe in operation. TSS Prevents atmospheric contamination (Dust and vapour) due to enclosed operation.
Key Features
Load Cell for synchronisation and auto line speed for maximum productivity
Stock level Sensors in Chute
SCADA & PLC
Hydraulic / Motorised Nip Adjustment with LVDT for Gap measurement
Large Hopper Chute
Special Features
Fixed with bolts over feed Barrel opening and customised to be connected at the bottom of the Mixer platform. Smart level sensors are provided to adjust the screw and roll speed according to batch weight from mixer. For visual inspection additional window are provided. Chute can maintain at least 3 batches of stock dumped from the internal mixer.
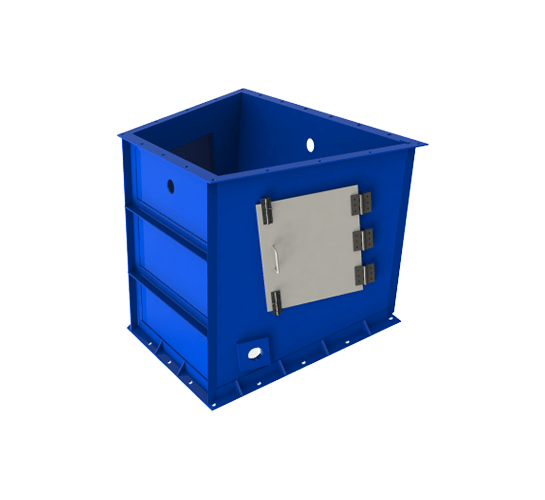
Counter Rotating, Conical & non-contact screws are supported by antifriction bearing in the gear housing. High wear resistant screws with hard chrome plated are offered. Special flight design gives a smooth flow of material in to the integral calendar. Shafts are drilled for cooling/heating to match dump temperature.
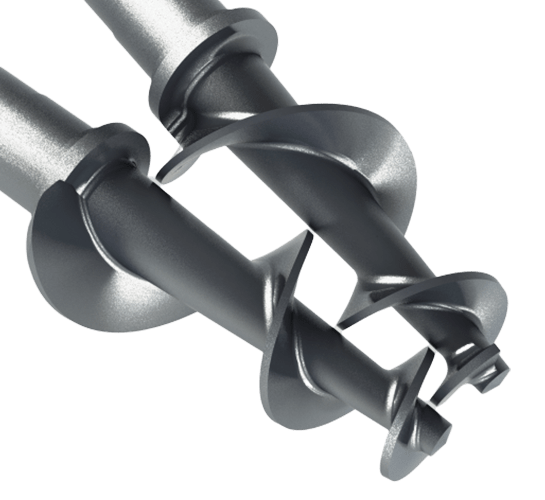
TSS is equipped with either motorised or hydraulic nip adjustment. LVDT enabled system gives precise nip gap adjustment.
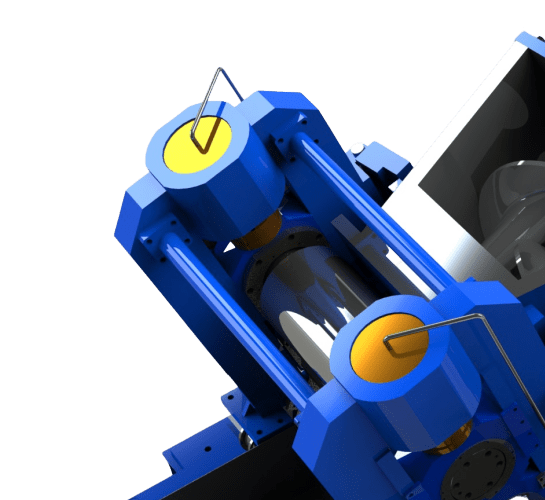
A specially designed split arrangement has been provided between calendar & extruder for easy maintenance.
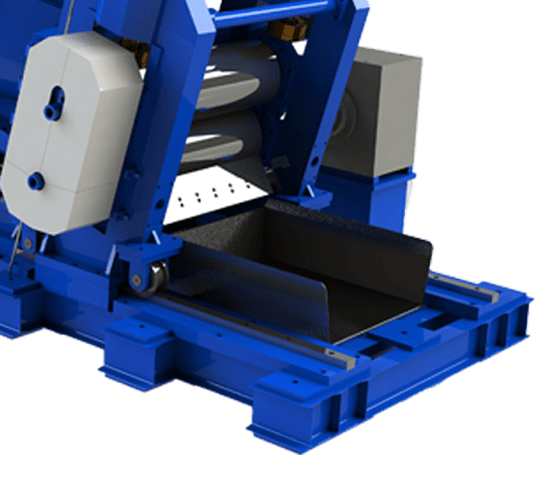
Downward Inclined design barrel, duly hard chrome plated, allows faster movement and complete unloading of dump towards rolls. Barrels are jacketed for effective cooling or heating.
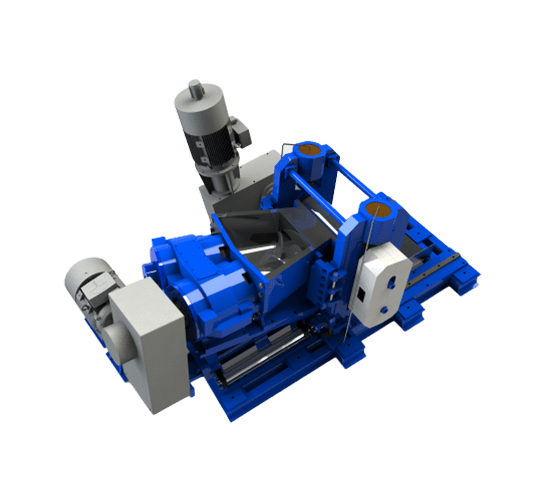
Best quality chilled cast iron peripherally drilled rolls ensure a precise and accurate sheet thickness.
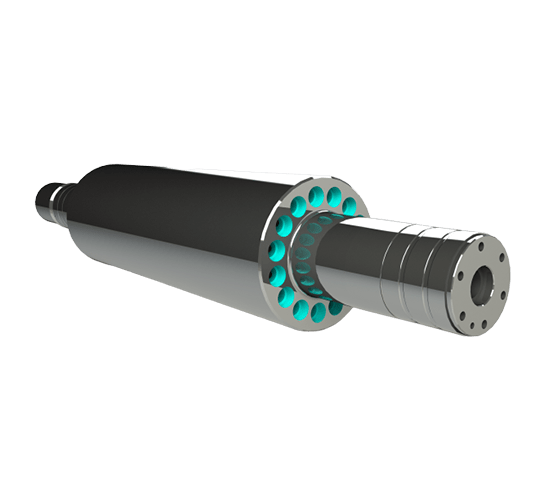
Complete assembly with bearing housings can be removed horizontally through frame windows for maintenance. Two hydraulic cylinders each side can be actuated electrically or manually (during power failure) for movement. Load cell at the discharge end of extruder is mounted for synchronization of screw speed with roll speed. Sensing excess load, through interconnected with control panel, will speed up Calender and maintain balance of material flow with speeds of extruder/Calendar.
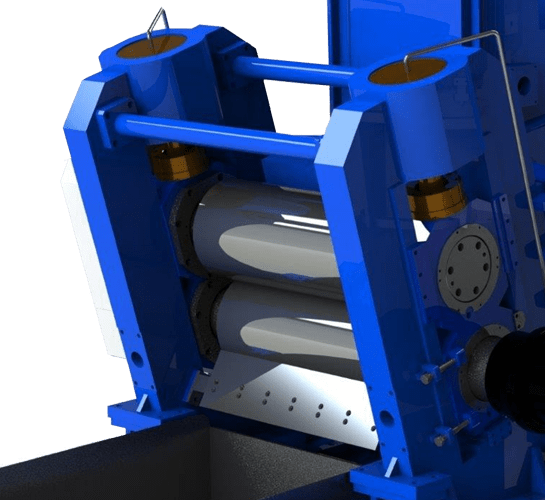
BM series Twin screw sheeter will be equipped with an intelligent drive system that will be inlined with parent mixer and batch off the cooling line to ensure efficient line speed change.
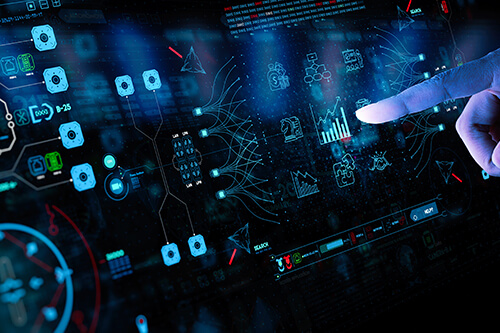
TSS Size | Mixer Suitability | |||
---|---|---|---|---|
2 Ton/Hr | 50 L | 70 L | 80 L | 95 L |
5 Ton/Hr | 120 L | 150 L | 160 L | 180 L |
9 Ton/Hr | 210 L | 240 L | 270 L | 310 L |
12 Ton/Hr | 330 L | 370 L | 440 L |
Safety Features